Tags: CNC | rapid prototyping Porovnání dvou technologií výroby fyzických prototypů
V současných podmínkách, při neustálém zkracování inovačních cyklů, představuje příprava prototypů významnou fázi procesu přípravy nového výrobku. Její kvalitní a rychlé zvládnutí umožňuje vyhodnotit širší spektrum možných variant řešení při posuzování designu a funkčnosti produktů, při zlepšování a zlevňováním výrobního procesu. Právě možnost relativně levného odstraňování skrytých vad a nedostatků výrobku již ve fázi návrhu umožňuje předcházet vysokým nákladům na odstraňování chyb v pozdějších fázích.
Fyzický prototyp je první materiálovou vizualizací výrobku, který se nachází ve fázi vývoje. Jeho úkolem je poskytnout praktické informace o funkčnosti, kvalitě, ergonomii výrobku a v některých případech slouží i pro získání informací o potřebných technologiích výroby a nákladech na výrobu. Při použití tradičních metod produkce je výroba prototypu poměrně zdlouhavá, spotřebuje velkou část času určeného pro celý vývoj výrobku. Důsledkem je, že v mnoha případech prototyp není k dispozici při řešení dalších kroků vývoje a při některých důležitých rozhodnutích. Dlouhá průběžná doba výroby prototypu je kromě jiných faktorů způsobena i vysokým podílem manuální práce. Nezanedbatelná je i nákladová stránka zhotovení prototypu. Včas zhotovený prototyp přitom představuje velkou marketingovou výhodu – je možné představit budoucí výrobek zákazníkům či prezentovat ho na výstavách, veletrzích apod. Článek je zaměřen na porovnání dvou možností výroby konkrétního prototypu při vývoji nových produktů, a to technologie známé pod názvem Rapid Prototyping (rychlá výroba prototypů) a technologie CNC frézování.
Rapid Prototyping je zatím nejběžnější název pro četné metody, které se používají k výrobě fyzických prototypů přímo ze zdroje dat, kterým je 3D CAD systém. Podstata všech metod spočívá v postupném přidávání materiálu až do dosažení konečného tvaru součásti. Navzdory názvu Rapid Prototyping samotný proces stavby součástky nemusí být velmi rychlý a nemusí nutně sloužit pouze k výrobě prototypů. Pokud se mluví o rychlosti, je myšlena spíše rychlost přípravy zhotovení součástky, protože je možné vyloučit některé procesy, které předcházejí zhotovení součástky klasickými výrobními metodami. Pokud se mluví o prototypování, v praxi se tato technologie zatím nejčastěji využívá při vývojových, konstruktérských a designérských činnostech, ale začíná se prosazovat i jako plnohodnotný výrobní prostředek na zhotovování sériových výrobků. Tato technologie je poměrně mladá, její praktické využití lze zatím počítat na roky. Opakem je číslicově řízený proces obrábění, vyvíjený a neustále zdokonalovaný desítky let. Základem je i v tomto případě 3D, méně často ještě 2D počítačový návrh budoucího výrobku. Proces tvorby je oproti RP technologiím opačný, z bloku polotovaru se postupným odebíráním materiálu vytváří konečný tvar součástky. Některá srovnání obou technologií- Použití RP je z hlediska tvarů výrobku téměř neomezené. Je možné vytvářet dutá tělesa nebo v jednom kroku celé funkční sestavy, sestávající z několika dílů. Obrábění je omezováno nutností zajistit přístup nástroje k místu vytváření potřebného tvaru. Některé tvary nejsou vůbec vyrobitelné, jako např. ostré vnitřní rohy (při frézování). Další nevýhodou je nutnost upnutí, často omezující přístup nástroje k obráběným plochám. Vyvolává to potřebu znovu upínat obrobek v jiné poloze.
- Při CNC obrábění je zřejmá závislost nákladů na tvaru součástky. Složité tvary vyžadují delší čas na přípravu řídícího programu, drobné detaily vyžadují malé nástroje s nízkou použitelnou hodnotou posuvu, což prodlužuje výrobní čas. Tyto faktory přispívají ke zvyšování nákladů. Při RP je cena většinou stanovována na základě množství spotřebovaného materiálu nebo na čase potřebném pro zhotovení výrobku.
- RP systémy mají výhodu v tom, že není nutné připravovat polotovar potřebných rozměrů a upínat ho na pracovní stůl stroje. Po ukončení procesu je ale třeba u některých metod očistit výrobek od podpůrných materiálů.
- Vytvoření NC programu je vázáno na využívání dalšího softwaru (CAM). Software pro RP zařízení je jeho součástí.
- Obrábět na většině CNC strojů lze všechny běžné konstrukční materiály. Výběr materiálů je tedy větší než u zařízení pro RP, která jsou z principu vázána na jeden materiál. K dispozici jsou četné plasty, keramika, kovy a papír.
- CNC obráběcí stroje jsou dostupné v různých velikostech, větší RP stroje zatím nejsou. Velké díly se v zařízeních RP zhotovují rozdělené na menší části, které je pak třeba spojit do jednoho celku, nejčastěji lepením.
- Ceny za high-end RP stroje jsou vysoké, ceny strojů určených pro tvorbu koncepčních modelů jsou nižší, ale stále poměrně vysoké. Podobná situace je i v oblasti CNC techniky. CNC systém (stroj a software) je finančně náročný, ale stále častěji se objevují malé stroje, často prezentované jako hobby zařízení, jejichž cena je velmi přijatelná. Jejich nevýhodou ale většinou je omezený sortiment použitelných materiálů (většinou jen snadněji obrobitelné materiály). Nenáročnost na umístění (nemusí to být dílenské prostory) je předurčuje i na výrobu prototypů.
- Jednotlivé metody Rapid Prototypingu, používané v praxi, se vzájemně liší mnoha kvalitativními i ekonomickými parametry, které následně určují míru vhodnosti použití jimi vyráběných prototypů pro jednotlivé aplikace.
- RP systémy nanášejí materiál v konstantní tloušťce, čímž je dána i výsledná přesnost součástky. Při použití CNC frézování vzdálenost mezi drahami nástroje je volitelná. Tato možnost volby přesnosti znamená možnost upřednostnění rychlosti nebo přesnosti výroby součástky.
Příkladem pro srovnání může být součástka pro funkční prototyp (obr. 1) – ozubená páka ve tvaru půlkruhu o průměru Ø 80 mm. Obr. 1 Tvar součástky Součástka byla zhotovena oběma technologiemi. Při využití 3osé CNC frézky čas výroby dosáhl 2 hod. 34 min. Jako nástroje byly použity stopkové frézy průměrů Ø 6,2 a 1 mm. Čas výroby mohl být kratší, ale rozsah otáček použitého stroje neumožňuje efektivně využívat nástroje malých průměrů. Přípravné práce, včetně tvorby řídícího programu, trvaly zhruba 3 hod. Není v tom zahrnut čas přípravy polotovaru, který byl dodán objednatelem v požadovaném tvaru (obr. 2). Materiálem polotovaru byl polyacetal POM. Celkový čas potřebný na stavební díly byl tedy cca 5,5 hod.
Obr. 2 Připravený polotovar pro CNC frézování
Potřebný NC program pro frézování polotovarů a dosažení požadovaného tvaru byl vytvořen v CAM systému SolidCAM. Sestava polotovaru a součástky v prostředí tohoto systému je na obr. 3. Navržený postup obsahoval hrubovací i dokončovací operace. Před samotným generováním NC kódu byl celý proces vizualizován (obr. 4), aby se předešlo chybám a kolizím při samotném frézování. Systém umožňuje provést analýzu přesnosti obrobení, což bylo také využito.
Obr. 3 Výchozí stav řešení v CAM systému – sestava polotovaru s obrobkem Obr. 4 Vizualizace průběhu obrábění v prostředí CAM systému Jako alternativní způsob výroby navrhované součástky byla zvolena jedna z metod Rapid Prototypingu, a to 3D tisk metodou FDM (Fused Deposition Modelling). Příprava 3D modelu je poměrně jednoduchá. Po načtení .stl souboru budoucího prototypu v programu Catalyst a nastavení požadovaných údajů software vygeneruje všechna potřebná data pro 3D tiskárnu (obr. 5). Následně se data sítí odešlou na zařízení a spustí se samotný proces výroby. Dosažený čas výroby 49 min. spolu s časem přípravy a kontroly 3D modelu (dalších asi 10 min.) byl cca 5krát menší než při CNC frézování. Zhotovené součástky nebyly dále vzhledově upravovány. Na dílu zhotoveném technologií RP byl hlavně na ozubení a otvorech viditelný způsob vrstvení materiálu, na některých místech byl materiál nehomogenní. Na povrchu součástky zhotovené frézováním byly pozorovatelné typické stopy po nástroji. Při kompletaci prototypu navrhovaného zařízení byla nakonec využita součástka zhotovená na CNC frézce. Hlavním důvodem bylo poměrně velké provozní zatížení součástky.
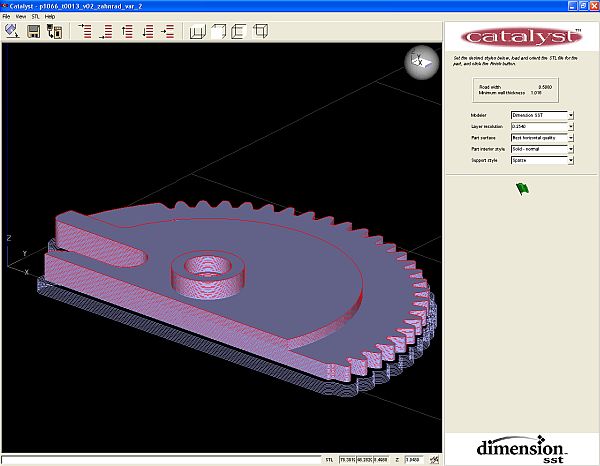 Obr. 5 Příprava dat v programu Catalyst ZávěrPopisované porovnání dvou technologií není možné zobecňovat na všechny případy. Rapid Prototyping zatím není řešením každého problému během vývoje a přípravy výroby výrobku. CNC technologie je rozšířená, ekonomická, nabízí široký výběr materiálů na frézování a dosahuje velmi dobrou přesnost. Přesnost metod Rapid Prototyping obecně zatím není tak dobrá jako u CNC obrábění, ale je přijatelná pro širokou škálu aplikací. Množství a vlastnosti materiálů používaných metodou Rapid Prototypingu jsou omezené a závisí na zvolené metodě. Avšak rozsah materiálů a jejich vlastností rychle roste. K dispozici jsou i mnohé sekundární procesy pro úpravu výrobků do konečné podoby. Je ale snadné hledat extrémní případy a na nich určovat, která technologie je lepší – CNC, nebo RP. Na výběr způsobu zhotovení prototypu má vliv řada faktorů, jejichž posouzení je na samotném pracovišti realizujícím vývoj nového výrobku. Obr. 6 Porovnání dílů zhotovených technologiemi RP (vlevo) a CNC (vpravo) Článek vznikl s podporou VEGA v rámci řešení grantové úlohy 1/4159/07 „Počítačová podpora výroby tvarově složitých ploch na CNC strojích pro výzkum, vývoj a ověřování nástrojů a forem na výrobu plastových automobilových součástek“.
Literatura- Slota, J.–Gajdoš, I.: The application of rapid prototyping, CAE and CAM methods in product development process. In: Scientific Bulletins of Rzeszów University of Technology: Mechanics 73. No. 253 (2008), str. 251–256.
- Kráľ, J., et al.: Obmedzujúce limity dnešných CNC obrábacích centier. Acta Mechanica Slovaca, Košice, 3A/2008, str. 219–222.
- Lennings, L.: Selecting Either Layered Manufacturing or CNC Machining to Build Your Prototype.
http://dutoce.io.tudelft.nl/~jouke/docdb/docs/rpm2000lennings.pdf - Budzik, G.–Sobolak, M.: Generating stereolitographic (STL) files from CAD systems. Acta Mechanica Slovaca, Košice, 2B/2006, str. 73–78.
- Józwik, J.: Prognozowanie odchyłek kształtu i wymiaru na podstawie sumarycznych, względnych przemieszczeń przedmiotu podczas obróbki. Przegląd Mechaniczny, 2005, č. 9, str. 106–109.
|