Tags: CAE K významným a náročným oblastem strojírenství se zařazuje i výroba řezných nástrojů. Řezný nástroj je aktivním prvkem výrobního procesu a jeho vlastnosti se výrazně projevují na kvalitě vyráběných součástek i ve výšce nákladů na jejich výrobu. Využívání CA technologií při návrhu řezných nástrojů tak představuje další vhodnou oblast pro jejich aplikaci.
Požadavky na řezné nástrojeK základním požadavkům na materiály řezných nástrojů patří tvrdost a její zachování za vyšších teplot, pevnost v ohybu, žáruvzdornost a žárupevnost, otěruvzdornost a odolnost vůči opotřebení. K těmto materiálovým požadavkům se přidávají i požadavky na tuhost nástroje, minimální deformaci vlivem silového a tepelného zatížení a další, kterých splnění je možné do značné míry ovlivnit jeho konstrukcí. Tu je možno optimalizovat už v prvních etapách jeho vzniku pomocí výpočetní techniky a s použitím vhodných prostředků navrhování, modelování a simulace.
Řezné nástroje jsou většinou tvarově velmi složité součástky a jejich komplexní konstrukční návrh umožnily až tzv. velké CA systémy, ke kterým patří např. Pro/Engineer, Catia apod. Tyto systémy umožňují vytvářet prostorové modely, ohraničené složitými obecnými plochami (obr. 1) a následně provést pevnostní a deformační analýzu návrhu, případně vyexportovat návrh přes některý z přenosových formátů do CAE systému, pracujícího na základě metody konečných prvků (MKP) - obr. 2.
Obr. 1 Prostorový CAD model monolitní válcové frézy 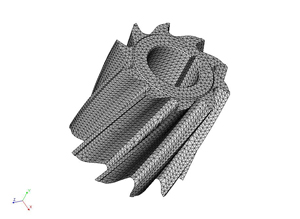 Obr. 2 Model frézy s vytvořenou sítí konečných prvků
Při konstruování řezných nástrojů se rozlišují dva základní přístupy, závislé na tom, zda navrhovaný nástroj bude monolitní, anebo bude využívat řezné destičky. Největší problémy se vyskytují při vytváření přechodových ploch na řezných klínech monolitních nástrojů, jako jsou například zubové mezery a jejich přechod do řezného klínu, podbrušování nástrojů apod. Návrh nástroje využívajícího řezné destičky je vázán na sortiment destiček a způsob jejich upevňování – obr. 3 a 4.
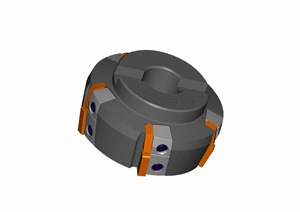 Obr. 3 Frézovací hlava s vyměnitelnými destičkami
Obr. 4 Způsob upevnění vyměnitelných destiček Jednou z výhod využívání CA systémů v dané oblasti je možnost přímo odvodit tvar činné části nástroje od tvaru zhotovovaného povrchu. Tento problém byl u tvarových nástrojů v minulosti řešen různými grafickými metodami anebo sestavováním matematických vztahů popisujících zhotovovaný povrch a následně odvozených vztahů pro popis řezné části nástroje. Zatížení řezného nástrojeZákladním předpokladem správného dimenzování nástroje je znalost velikosti, směru a smyslu vnějších sil působících na nástroj. Velikost těchto sil je závislá na podmínkách obrábění a je možné je určit výpočtem anebo měřením. V nástroji působením těchto vnějších sil (ke kterým můžeme přidat i upínací síly) vznikají napětí. Je známo několik teoretických modelů popisujících rozložení zatěžujících napětí od řezných sil na kontaktních plochách nástrojů. Podle charakteru působících sil je možné rozlišit zatížení statické nebo dynamické. Dynamické zatížení je obvykle rázové a cyklické, měnící se v krátkých časových intervalech a s velkým zrychlením. Příkladem dynamicky zatěžovaných nástrojů mohou být frézovací nástroje. Charakteristická namáhání řezných nástrojů při statickém zatížení: - Namáhání tahem – vyskytuje se nejčastěji u protahovacích nástrojů. Kontrola na pevnost v tahu se vykonává v jejich nebezpečném průřezu. Čistý tah vzniká jen u nástrojů souměrně zatížených vzhledem k jejich ose.
- Namáhání na tlak – vyskytuje se především u protlačovacích trnů a kontroluje se v jejich nejmenším průřezu. Pro dlouhé a štíhlé nástroje se provádí i kontrola na vzpěr. Ztrátou stability jsou ohroženy i vrtáky.
- Namáhání na krut – je charakteristické například pro závitníky a vrtáky. Při malých posuvech se zanedbává osová síla a provádí se jen zjednodušená kontrola na namáhání čistým krutem.
- Namáhání na ohyb – namáhání čistým ohybem je u řezných nástrojů zřídkavé, ale používá se při zjednodušené pevnostní kontrole soustružnických nožů, při pevnostní kontrole zubů nástrojů s vícerými řeznými klíny apod.
- Kombinované namáhání – kombinace namáhání tlakem, krutem a ohybem se vyskytuje u vícerých typů nástrojů (nůž pro vnitřní soustružení apod.).
U některých nástrojů se řezná síla v procesu obrábění mění jen málo a je možné předpokládat, že jsou vystaveny statickému namáhání. U jiných nástrojů anebo u jejich částí (soustružnický nůž při přerušovaném řezání, zuby frézy) průběh namáhání v závislosti na čase má mizící charakter a v těchto případech je porovnávací hodnotou pro provozní namáhání namísto meze pevnosti mez únavy.
Při návrhu a pevnostním výpočtu monolitního řezného nástroje je potřebné zohlednit i možné zeslabení jeho kritického průřezu vlivem přeostřování řezného klínu. V tomto případě se stanovuje minimální dovolený průřez, který ještě unese provozní namáhání nástroje. V zájmu optimálního využívání řezných nástrojů je sledovaným parametrem jejich opotřebovávání. Opotřebení řezného nástroje vzniká interakcí mezi nástrojem a materiálem obrobku a je ovlivněno řeznými podmínkami. Opotřebení je produktem kombinace zatěžujících faktorů působících na řezný klín. K nejvýznamnějším patří mechanický, tepelný, chemický a abrazivní faktor. Při mechanickém zatížení jsou při statickém i dynamická zatížení, odvíjející se od procesu utváření třísky anebo vznikající vlivem nekonstantních řezných parametrů, či přerušovaným řezáním. Při řezání vzniká velké množství tepla a následné tepelné zatížení značně namáhá materiál řezného klínu. V některých případech, například při přerušovaném řezání, se vytváří dynamický faktor v okamžicích vstupu a výstupu řezného klínu do/z obráběného materiálu. Faktor chemického působení vyplývá z procesu tvoření třísky za vysokého tlaku a teplot, což způsobuje vytváření čistého kovového povrchu, který má sklony k chemickým reakcím a difúzním procesům. Většina obráběných materiálů obsahuje tvrdé částice různého druhu, které vyvolávají na nástroji abrazivní efekt. Kombinace těchto základních zatěžujících faktorů působí negativně na materiál činné části nástroje a narušuje ho.
MKP systémy při návrhu řezných nástrojůPři simulaci zatížení řezného nástroje využitím metody konečných prvků je nástroj nahrazen modelem, složeným z konečných částí (prvků). Přesnost simulace závisí na jemnosti a tvaru použitých konečných prvků. Doporučení pro volbu konečných prvků jsou uváděna v různých pramenech. Některé vstupní veličiny, které jsou pro simulaci nezbytné (např. pevnost, tvrdost, tepelná vodivost, součinitel tření, mechanické a tepelné zatížení) nejsou stanovitelné úplně přesně. Vzhledem k uvedeným skutečnostem jsou získané výsledky z matematického hlediska přibližné, ale z hlediska praktického, při správném postupu řešení, je chyba zanedbatelná. CA systémy s integrovanou MKP jsou využitelné i při posuzovaní odolnosti nástrojů vůči opotřebení a poškození. Opotřebení nástroje je možné na základě rozsáhlých výzkumů poměrně dobře predikovat a predikci opotřebení řezných nástrojů s využitím CAE systémů se v odborné literatuře věnuje poměrně hodně pozornosti. Poškození nástroje například vylomením části řezné hrany anebo zlomením řezného klínu je však zatím běžnými prostředky obtížně předpověditelné. Přehled vstupních údajů pro využití MKP je uveden na obr. 5. Východiskem pro analýzu napěťových stavů řezných nástrojů jsou experimentálně získané údaje z řezných zkoušek a vypočítané hodnoty podle ověřených vztahů. Příkladem experimentálně získaných údajů jsou záznamy hodnot řezných sil v závislosti na čase ze zkoušek zapichovacích soustružnických nožů. Obr. 6 zobrazuje záznam hodnot sil během zhotovování zápichu na součástce, na obr. 7 je detail na část záznamu v časovém intervalu 0–0,1 sekundy. Na obr. 8 je znázorněna část destičky zapichovacího soustružnického nože se zobrazeným průběhem napětí. Získaná napětí odpovídají mechanickému zatížení řezného klínu bez uvažování vlivu teploty.
Kromě rozložení napětí v tělese nástroje dovoluje MKP řešit problémy změny tvaru nástroje během jeho činnosti. Po stanovení mechanického a tepelného zatížení nástroje během řezání je možné určit velikost jeho deformace. To umožňuje stanovit vliv navrženého nástroje a zvolených řezných podmínek na přesnost zhotovovaného povrchu. Vizualizace deformace zapichovacího soustružnického nože je na obr. 9 (deformace je zvětšená kvůli lepší názornosti), obr. 10 zobrazuje velikost deformací v jednotlivých částích nástroje.
 Obr. 5 Vstupní údaje pro návrh řezných nástrojů v systémech MKP
Obr. 6 Záznam průběhu řezných sil pro zapichovací soustružnický nůž
Obr. 7 Záznam průběhu řezných sil v časovém intervalu 0–0,1 s
Obr. 8 Rozložení napětí v destičce zapichovacího soustružnického nože
Obr. 9 Vizualizace deformace zapichovacího soustružnického nože
Obr. 10 Znázornění deformace zapichovacího soustružnického nože ZávěrVzhledem k časové náročnosti a finanční nákladnosti řezných zkoušek nástrojů se do popředí stále víc dostávají prostředky modelování a simulace. Jejich konečným cílem je nahrazení technologických experimentů výpočtem. CA systémy tak svými možnostmi výrazně přispívají ke zkrácení doby potřebné na vývoj a výrobu nástrojů. Navzdory velkému sortimentu nabízených řezných nástrojů jsou ve výrobě žádané i speciální operační nástroje, určené hlavně pro zhotovování složitých ploch, obrábění na nepřístupných místech, nebo pro rychlou výrobu tvarových ploch na větším množství součástek. I v této oblasti mají CA systémy významné postavení – zkracováním vývoje takových nástrojů se zkracuje i celý proces přípravy výroby nového výrobku. Při výrobě tvarově podobných součástek, při jejichž návrhu se využila parametrizace, může být navazujícím krokem parametrizace celého procesu tvorby CAD modelu řezného nástroje. Další vývojový stupeň představuje využití specializovaných modulů CA systémů založených na znalostním inženýrství, do kterých je možné implementovat získané poznatky a zkušenosti pro využití při dalších řešeních.
Výsledky práce byly dosaženy řešením grantového projektu VEGA 1/4159/07 „Počítačová podpora výroby tvarovo zložitých plôch na CNC strojoch pre výskum, vývoj a overenie nástrojov a foriem na výrobu plastových automobilových dielcov“. Literatura- Řasa, J. : Výpočetní metody v konstrukci řezných nástrojů. SNTL/ALFA Praha, 1986.
- Jandečka, K.–Mourek, D.–Kapinus, V.: Moderní využití CA-technologií při vývoji nových řezných nástrojů. In: Nástroje 2003, Zlín, 2003.
- Leopold, J.: Werkzeuge für die Hochgeschwindigkeitsbearbeitung. Carl Hanser Verlag München– Wien, 1999.
- Ondra, J.: Využití simulace řezného procesu při obrábění. In: Technológia 2003, Bratislava, 2003.
- Altan, T.–Yen, E.: Modeling of metal cutting using FEM. In: CIRP Workshop on FEM Modeling of Machining Operations, Paris, 2003.
- Žarnay, J.: CA technológie pri návrhu rezných nástrojov. KTaM SjF TU v Košiciach, 2004, Košice.
Autoři pracují na SjF TU v Košicích. |